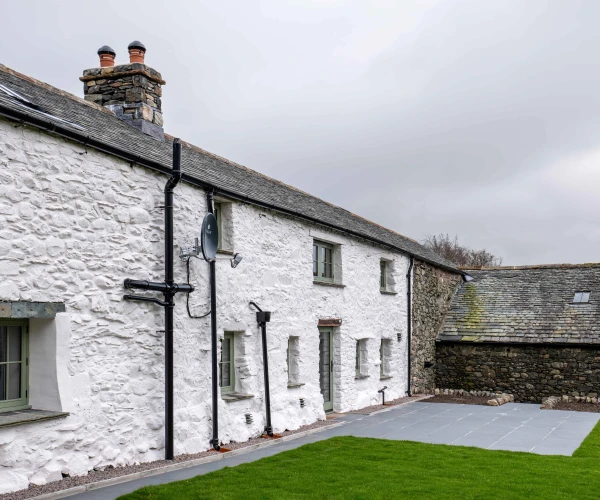
Featured
Ullswater Cottage Renovation
A traditional stone barn on an exposed Cumbrian hillside has been transformed fr...
A traditional stone barn on an exposed Cumbrian hillside has been transformed fr...
Barry McCarron, Chair of the Passive House Association of Ireland, and his famil...