Go to Section
Construction and the Climate Debate: How Can the Industry Make Faster Progress?
Friday 2nd October 2020
Also in category: Retrofit
As part of the United Nations Framework Convention on Climate Change (UNFCCC), many countries including the UK and Ireland agreed to work as part of a global response to limit the global temperature rise to no more than 2 Degrees above pre industrial levels, but we set our targets hopefully lower at 1.5 Degrees above pre industrial levels.
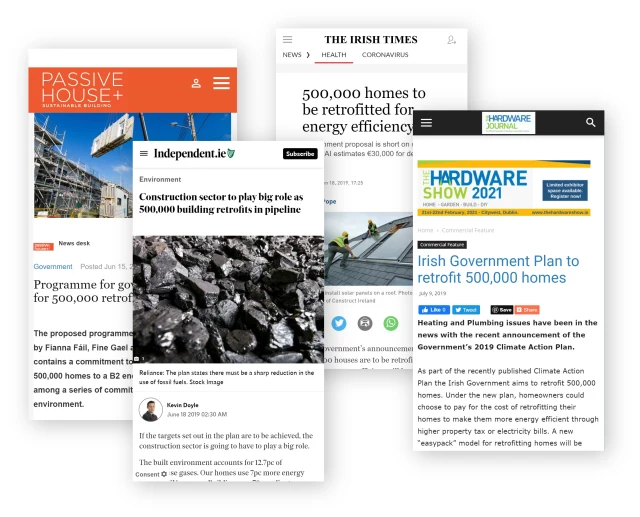
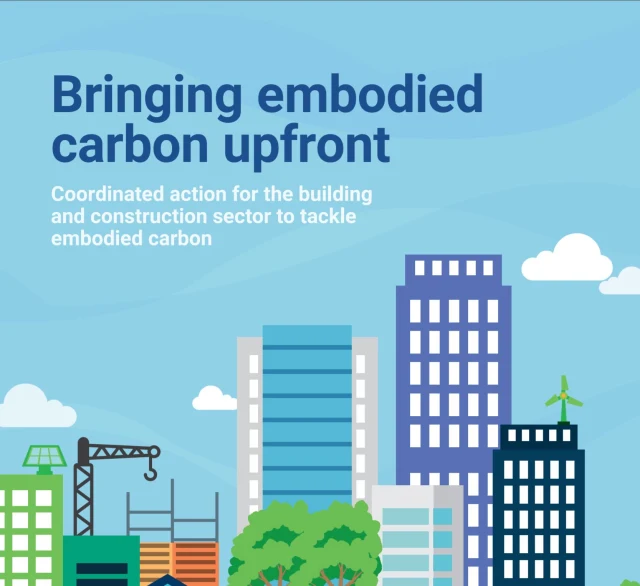
Blog author
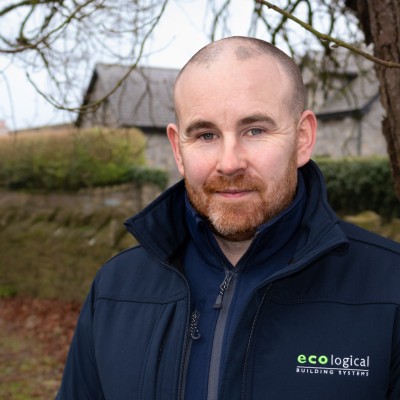
Joe Fitzgerald
Technical Specification Manager
Joe is a Passivhaus Contractor with Degree qualifications in Sustainable Construction and Energy Management. He also completed Postgraduate Diplomas in Green Engineering and Advanced Thermal Modelling and a Postgraduate Certificate in Hygrothermal Risk Assessment.