Go to Section
A Townhouse Case Study: Thermally Upgrading A Traditional Build
Tuesday 26th July 2022
Also in category: Retrofit
In the wise words of William Morris, founder of SPAB, "We are only trustees for those who come after us". There is a wealth of traditional buildings scattered across the Irish countryside, each with its own unique traits and thumbprint. What is common in many of these buildings, however, is that they are made of solid stone or brick walls which have trialled the test of time. That was the case with this dilapidated period townhouse in Carlow which was renovated using Diasen thermal plaster.
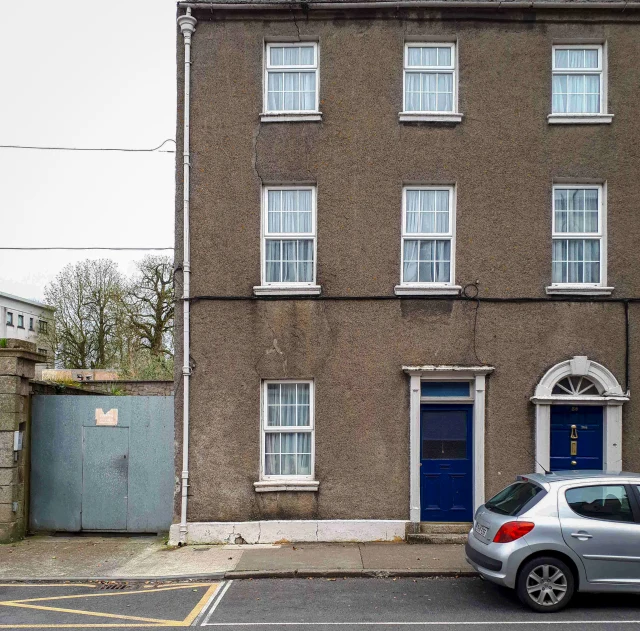
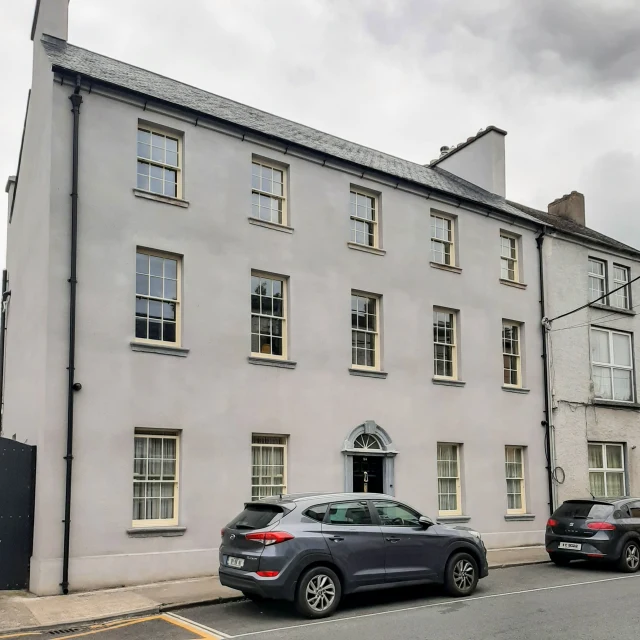
Blog author
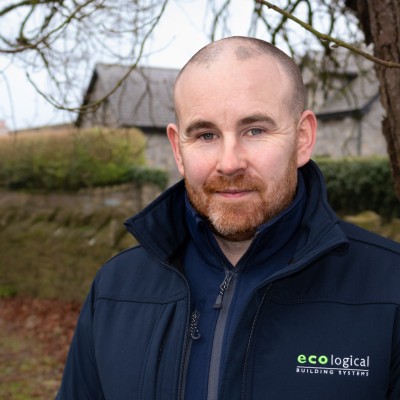
Joe Fitzgerald
Technical Specification Manager
Joe is a Passivhaus Contractor with Degree qualifications in Sustainable Construction and Energy Management. He also completed Postgraduate Diplomas in Green Engineering and Advanced Thermal Modelling and a Postgraduate Certificate in Hygrothermal Risk Assessment.