Go to Section
Thermal Comfort: A Natural Approach
Wednesday 11th September 2019
Also in category: House insulation, Retrofit
One of the huge challenges facing social housing providers is the need to reduce fuel poverty amongst tenants, particularly in thermally inefficient, older properties.
Much has been done to improve energy efficiency across the social housing asset base, but energy saving measures are only part of the solution to driving down bills and enhancing comfort.

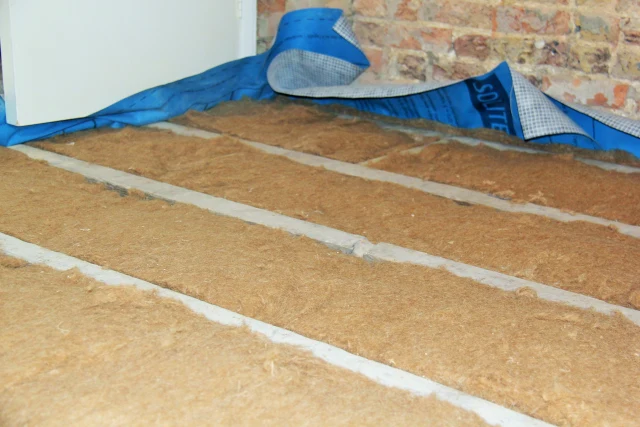
Blog author

Fintan Wallace
Architectural Technologist (Bsc Hons, CEPHC, CEPHT)
Fintan Wallace is an Architectural Technologist at Ecological Building Systems. Graduating from Dublin Institute of Technology in 2011 with a B.Sc (Hons) in Architectural Technology, it was here in D.I.T’s Bolton Street where Fintan developed a strong interest in low energy and Passivhaus design. From here he continued his studies becoming both a Certified European Passivhaus designer and tradesperson. Fintan has travelled to Baden Württemberg in Germany to study passive housing and sustainable energy technology, gaining significant knowledge regarding the use of natural insulations in timber frame and solid wall constructions. Fintan has been involved extensively in a deep energy retrofit of a property to the Enerphit standard in the west of Ireland and now advises on numerous projects throughout the UK for newbuild and retrofit.