Go to Section
COP 26 and the Importance of Sustainable Construction
Friday 29th October 2021
Also in category: Airtight and windtight, Healthy living, Company News
On the eve of the COP 26 Climate Emergency Conference in Glasgow, the current impending fuel crisis and the escalating debate on retrofitting homes to higher energy performance standards, Neil Turner from Ecological Building Systems discusses the importance of sustainable construction and its key role in terms of not only reducing the nation’s CO2 emissions, but ensuring that we can live in high performing, healthy, durable and energy efficient homes.
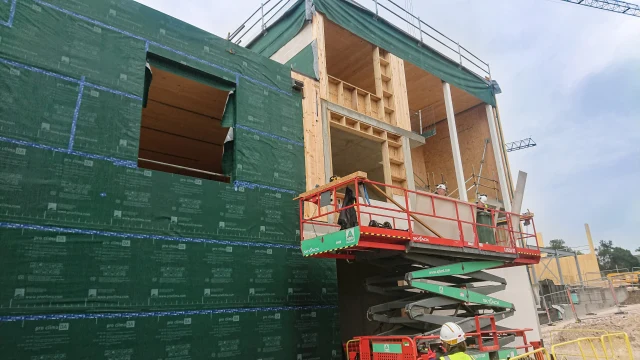
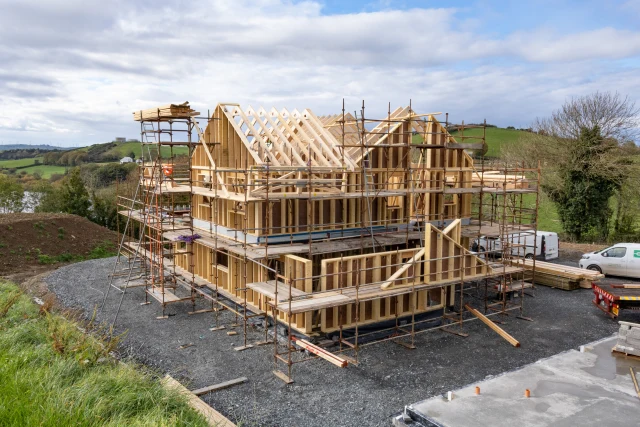
Blog author
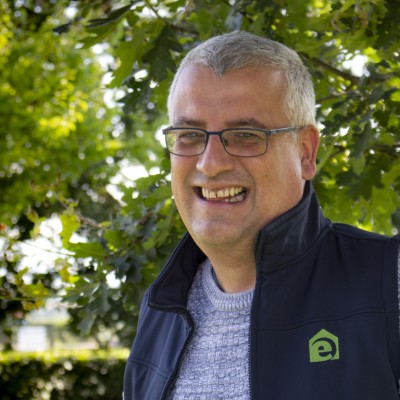
Neil Turner
UK Technical Manager (BSc Hons)
Neil Turner is Technical Manager at Ecological Building Systems. A former competent person of the BBA/TIMSA U-Value and Condensation Risk Calculation Competency Scheme, who has been involved in developing CEN (Comité Européen de Normalisation) European standards, Neil has extensive experience in the building products sector. Neil advises architects, contractors and timber frame specialists on the specification of sustainable insulation products and has been involved in numerous sustainable projects throughout the UK.