Go to Section
A Best Practice Approach To Insulating Suspended Timber Floors
Thursday 14th February 2019
Also in category: House insulation, Retrofit
Fintan from our Technical Team discusses the thermal loss issues associated with suspended timber floors and outlines a best practice approach to tackling them.
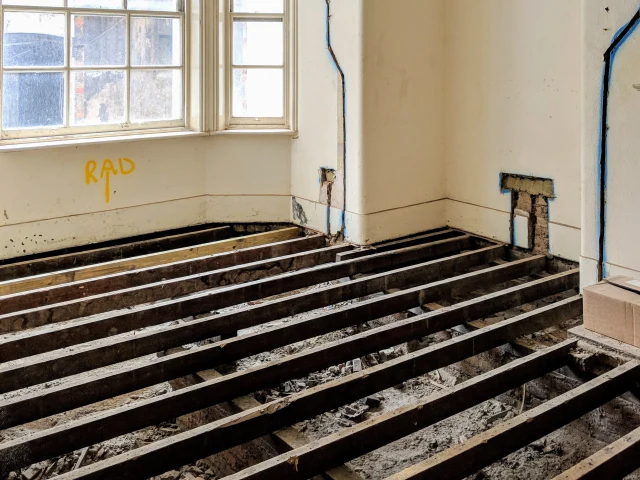

Blog author

Fintan Wallace
Architectural Technologist (Bsc Hons, CEPHC, CEPHT)
Fintan Wallace is an Architectural Technologist at Ecological Building Systems. Graduating from Dublin Institute of Technology in 2011 with a B.Sc (Hons) in Architectural Technology, it was here in D.I.T’s Bolton Street where Fintan developed a strong interest in low energy and Passivhaus design. From here he continued his studies becoming both a Certified European Passivhaus designer and tradesperson. Fintan has travelled to Baden Württemberg in Germany to study passive housing and sustainable energy technology, gaining significant knowledge regarding the use of natural insulations in timber frame and solid wall constructions. Fintan has been involved extensively in a deep energy retrofit of a property to the Enerphit standard in the west of Ireland and now advises on numerous projects throughout the UK for newbuild and retrofit.