Go to Section
How to insulate your loft with natural insulations
Friday 9th September 2022
Also in category: House insulation, Retrofit
How can recycled wood chips, carbon-negative production process hemp and recycled coffee and cocoa bean sacks help keep you warm and reduce your carbon footprint? The answer is: loft insulation!
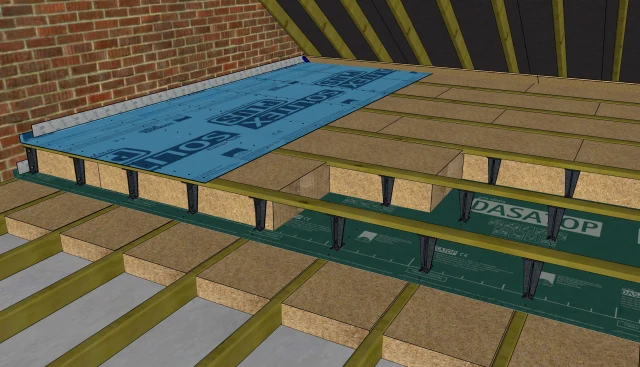
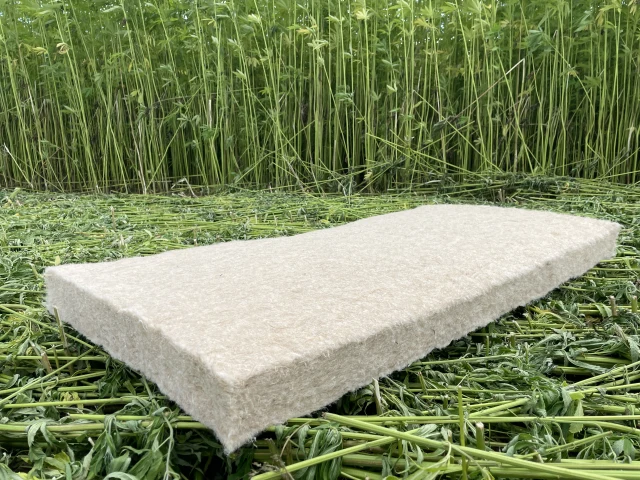
Blog author
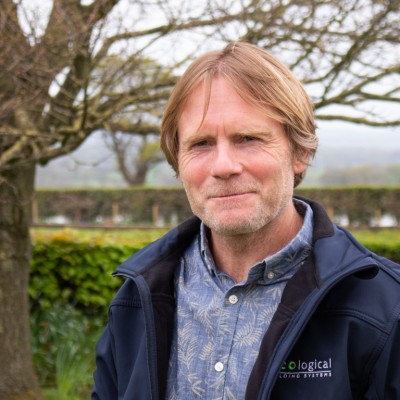
Dave Judd
Technical Specification Advisor (BSc Hons, MSc)
Dave has extensive experience with energy efficiency retrofits and is well acquainted with the “fabric first” principles of integrating airtightness and insulation in both new-build and existing buildings. He has also worked within the domestic renewable energy sector, with the main emphasis on solar PV, solar thermal and biomass systems. He has a Degree in Environmental Science and an MSc in Architecture: Advanced Environment & Energy Studies and recently qualified as a Certified Passive House Tradesperson with the Passive House Institute. Outside of work, Dave enjoys trail running and cycling, growing vegetables and being sociable.